Machine Control – Roads
Optimised 3D surveying and surfacing workflow
The Challenge
The traditional surveying process for road resurfacing is time consuming and can result in expensive errors. Conventional workflows would typically involve hammering pegs into the ground every five metres longitudinally and then measuring the transverse profile every 10 or 20 metres, evaluating the data, drawing up marking schedules and ensuring that all the relevant data is documented. Costly traffic management and road closures are required, which can lead to heavy traffic jams, frustration and in some cases road worker abuse. When using traditional paving techniques, often an inlay resurfacing job results in the same uneven road surface being milled out and paved back again as the longitudinal profile has not been adequately smoothed out.
The Solution
The Machine Control workflow eliminates the need for lane closures. R3 can quickly scan miles of road in a short time, without the need for traffic management, instantly capturing millions of data points of the existing surface. This data is used to optimise the design to produce a more even, less bumpy road surface and improve cross slopes whilst reducing material usage and the number of on-site personnel working in danger zones.
Having a detailed 3D model of the existing surface in advance of works commencing allows successful planning for accurate material calculations and eliminating guesswork for quantities of asphalt or milling required. Machine Control is the perfect tool for mainline paving or milling projects requiring long sections of road that need resurfacing. This complete workflow allows you to stay productive and be ahead of schedule.
Variable depth milling
- Identify existing asphalt surface profiles
- Eliminate guesswork and bid your job accurately
- Increase productivity and mill only what’s necessary
- Mill one time and deliver a more even, less bumpy surface for a perfect paving job
Variable thickness paving
- Quickly and safely scan roads to generate a 3D model of existing surface
- Create design to meet longitudinal evenness and cross slope expectations
- Manage materials to stay within acceptable yields
- Maximise productivity while reducing manpower,equipment hours and overheads
Benefits
Safety
- No survey crews required to survey the existing ground level in live traffic. This means no employees at risk during data collection surveys
- Safer system of work for on-site personnel
- Less risk of personnel/plant conflict
- Safer driving conditions for the road user
Environmental
- More even road profile and improved IRI/RI
- Reduced rolling resistance which results in less fuel consumption
- Reduced unnecessary over-milling of existing material
- Reduced unnecessary over-use of asphalt materials
- Major opportunities for measurable carbon savings
Quality
- Removal of optical instrument errors in work practices
- Less structural damage from a more even
longitudinal profile increases the life span of the surface - Smoother and more comfortable driving experience for the road user
- Optimised design in the digital environment
- Data captured during workflow can be used for BIM or As-Built purposes
Cost savings
- LiDAR Data Collection v Conventional Methods
– Safer
– Faster
– Less expensive - More data collected for design
- Accurately calculate mill and fill quantities
at design stage - Only need 1 no. Total Station for compliance checks
Other Services
Runways
R3 provide standard testing services for airport Pavement Management Systems (PMS) as well as specialised testing for runways around the globe.
Racetracks
Contact Us
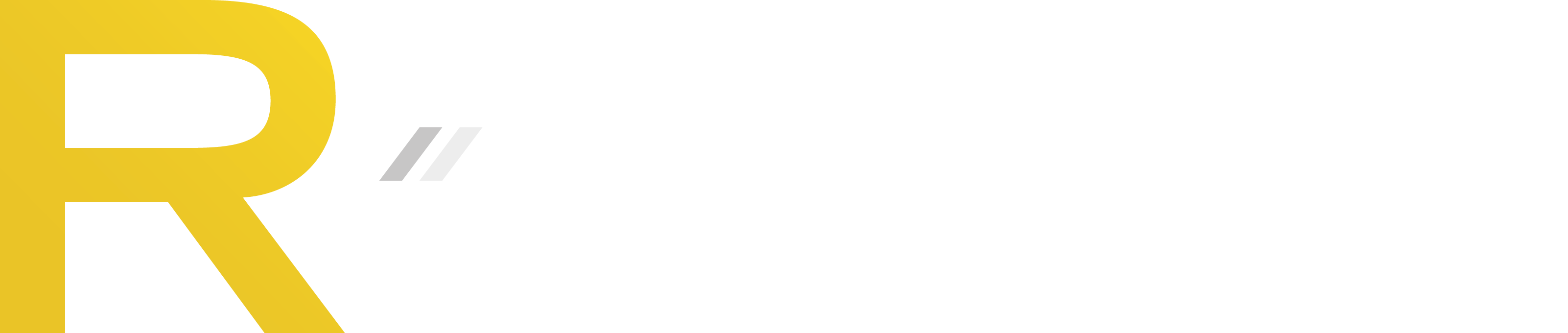
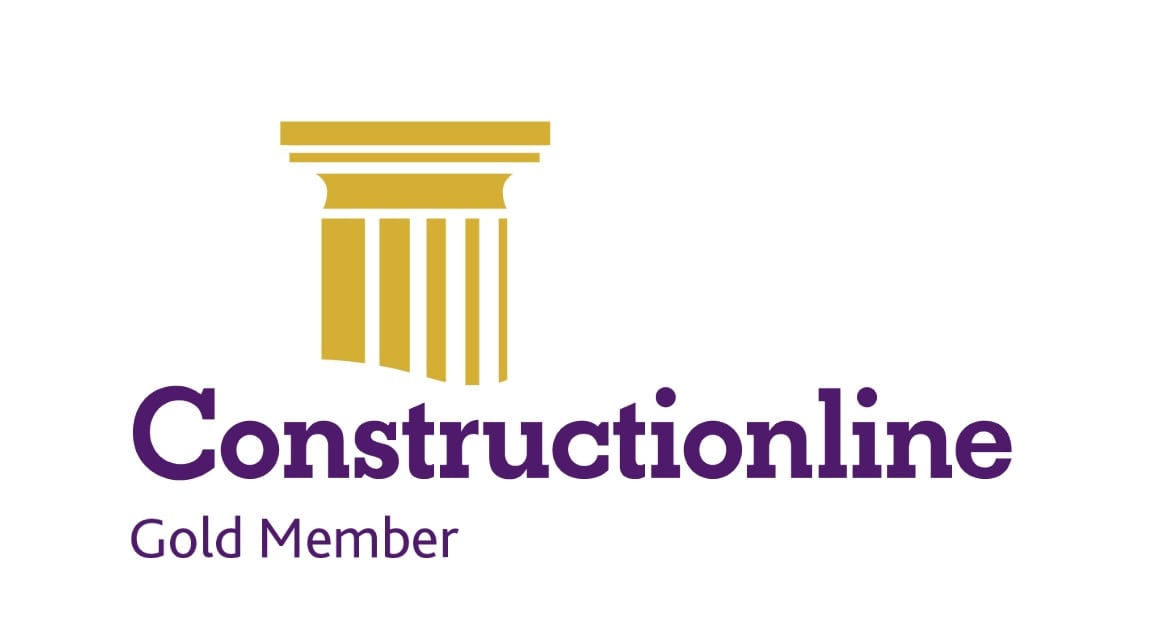