Who?
R3 were appointed by Aggregate Industries on the direction of the client and owner of Donington Park Circuit, Motorsport Vison (MSV) to provide LiDAR scanning and Machine Control files for the resurfacing at Donington Park Circuit.
R3 were also engaged by MSV and the track designer’s Driven to produce the specification of works and material specification. This also included providing Quality Assurance services during construction.
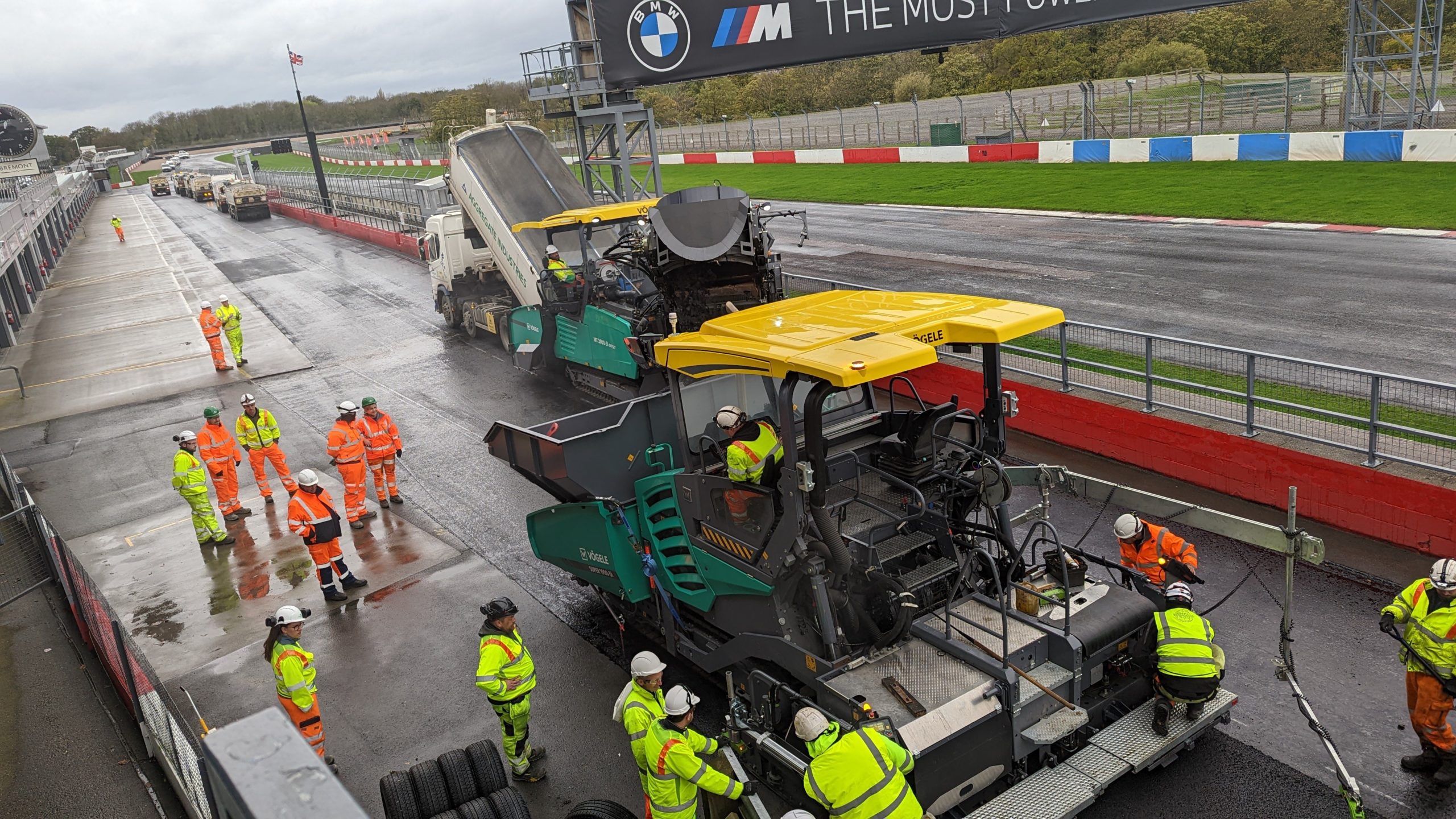
What was the challenge?
There was initial resistance from the supply chain to adopt the specification for works and the general methodology. What was requested is best practice for racetracks and has been used for FIA Grade 1 circuits by R3 elsewhere but is new technology and practise for the UK highways. This included the use of machine control for automating the milling process.
Donington Park is a historic circuit where changes and adaption have been made over the last 80 years. As such, there are issues with the kerbs where asphalt has been placed over older kerb systems. This meant that it was unclear what was in the lower layers under the surface course. MSV did not want to remove and reinstate new kerbs, so the resurfacing project had to tie in with the kerb lines.
What was the solution?
Working with Driven International, R3 started the process in January 2022 by creating a specification of works that included the construction methodology. This leaned on experience working with other tracks around the world utilising technology and processes that have not been used extensively on roads in the UK. The methodology specified the use of Topcon’s Smoothride workflow and Machine Control to automate the milling process. As Donington Park is used for both cars and bikes, racetrack smoothness had to be optimised with a strict tolerance of ± 3mm over 4m to ensure there are no bumps or undulance’s to provide a super smooth racing surface.
The material specification included the need for high quality aggregate and bitumen appropriate for use on a worldclass racing circuit. The asphalt specification was designed to provide optimum performance of grip and texture to ensure a safe surface for professional motorsport. How a tyre interacts with the surface was considered as part of this process.
The track designer, Driven International, compiled the specifications along with their drawings for the reprofiling of the track which included changes to cross-slopes and transitions.
Aggregate Industries were appointed as the principal contractor for the works. Aggregate Industries worked with Power Plane to deliver the milling and Wirtgen who supplied three new Vogele Pavers and Material Transport Vehicle’s (MTCs) for the project.
Upon commencement of the works in November 2023, we conducted a LiDAR scan of the entire track. The point cloud data was compared to previous scans and the Driven International design. This was used to produce 3D Machine Control files for the variable depth milling process. Working with Topcon’s European Specialist Paving Division and Power Plane a program for milling the track began. This involved a two milling pass methodology whereby the second pass used micro-milling to get a fine milled finish. The result was a reprofiled surface that was smooth enough to race on.
The construction of the new surface course was completed using three new Vogele Pavers running in echelon. Aggregate Industries designed the surface course material, Super Prixmat using a high PSV aggregate in accordance with the R3 specification and supplied from their nearby asphalt mixing plant. The proprietary SMA was designed specifically for racetrack performance.
The 40mm surface course was applied without the use of 3D Machine Control as the work have been done in the milling process. This methodology was selected as it allows for the smoothest surface course to be constructed.
There were issues with the kerb height of the new asphalt. This was a result of the existing kerbs and the methodology pushing the construction process to the very limits of the technology. The smoothness of the surface course was prioritised and working with the supply chain a solution was delivered balance the kerb levels.
Working with Driven International, R3 Engineers helped to oversee the construction process from a Quality Assurance perspective. This included working with Aggregate Industries and the supply chain to overcome any issues onsite while ensuring the specification was being met.
The result is a new asphalt surface that has consistent surface characteristics and is exceptionally smooth ready for worldclass motorsport. The first WSBK test had riders 0.2 seconds off the dry lap record running in wet conditions. Initially comments from the TCR series race was that the new surface has incredible grip everywhere in the dry and is around 1 second a lap faster than 2022.