Case studies
A889 | Setting a new benchmark in UK road surfacing
Category | Roads |
---|---|
Project | A889 Dalwhinnie Resurfacing |
Client | Transport Scotland |
Principal Contractor | BEAR Scotland |
Surfacing Contractor | Breedon |
Milling Contractor | EJ Douglas + Sons |
Partners | Topcon SmoothRide |
Date | October 2024 |
Solution(s) | Machine Control |
Project Overview:
BEAR Scotland engaged R3 Ltd to lead a groundbreaking road resurfacing project on the A889 near Dalwhinnie, delivering a UK-first using digital construction methods.
In collaboration with contractor Breedon, the project deployed Topcon’s SmoothRide workflow and machine control technology, integrated directly into the milling machine, to achieve exceptional accuracy. This precision not only enhanced surface quality by 41% but also enabled material predictions within 5% of actual usage — reducing waste, cutting costs, and supporting long-term sustainability gains.
±5% Material Prediction Accuracy
41% IRI Reduction
Lower Maintenance Costs
The Challenge
The project presented a number of complex challenges that demanded a strategic and innovative response.
- The existing road surface had a highly irregular profile, rendering traditional resurfacing methods ineffective
- Multiple areas exhibited water pooling and inadequate surface drainage, highlighting deeper structural concerns
These conditions made it clear that a standard approach wouldn’t suffice — a bespoke, data-led solution was essential to meet the unique demands of the site.
Project Goals
- Improve surface smoothness and road quality
- Minimise traffic disruption on a key Highland route
- Deliver precision through fully digital planning and execution
- Extend asset life while lowering long-term maintenance costs
What was the solution?
R3 replaced traditional resurfacing methods with a fully integrated digital workflow, combining Topcon’s SmoothRide technology and the RD-M1 LiDAR scanning system — a proven approach trusted on F1 racetracks and international airports for its unmatched precision and performance.
- High-Speed LiDAR Scanning: Captured detailed surface data at traffic speed, eliminating the need for full closures.
- Digital Twin Creation : Generated a precise 3D model of the road, enabling optimal design for smoothness, drainage, and material use.
- Automated Variable-Depth Milling : Executed resurfacing to mill only where needed, reducing material usage, waste, and margin for error.
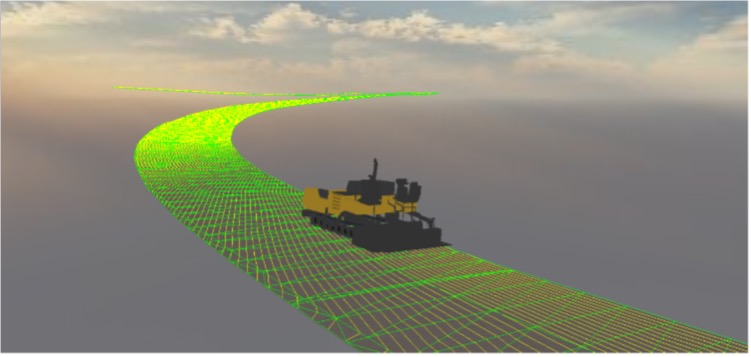
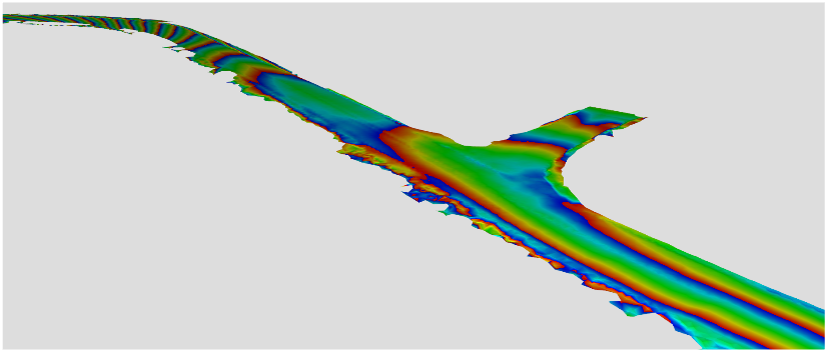
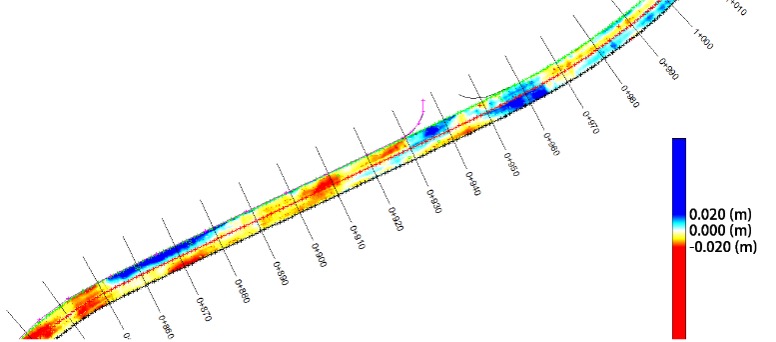
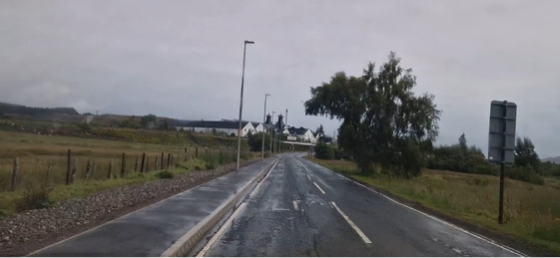
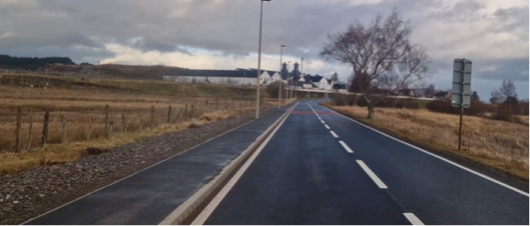
The Outcomes
This project marked a significant shift from traditional resurfacing methods to a fully digital workflow — reducing material usage and future maintenance needs. Delivered with minimal disruption, it achieved a 41% improvement in surface smoothness (IRI) and long-term value for both road users and asset managers.
Benefit | Impact |
---|---|
Reduced Material Use | Efficient, data-driven milling with machine control enabled material predictions within 5% accuracy — reducing waste, cutting costs, and lowering CO₂. |
Lower Maintenance Costs | Smoother surfaces and reduced wear mean fewer potholes, repairs and interventions over time. |
Improved Surface Quality | The road’s International Roughness Index (IRI) improved by 41% (before: 2.48 km/m, after: 1.46 km/m). |
Minimal Disruption | No full closures; data capture completed in live traffic. |
Sustainability Gains | Lower emissions, reduced waste, and longer-lasting surfaces. |
Fuel Efficiency Gains | Improved surface smoothness reduces rolling resistance, lowering fuel consumption for vehicles. |
Extended Asset Life | Less surface vibration reduces structural stress, leading to a more durable surface and extended lifespan. |
Improved Safety & Efficiency | Automated survey and design process limited the need for on-site personnel, lowering health & safety risks. |
Insights for Future Planning | High-resolution data and digital twin can be reused for asset management, maintenance forecasting, and future upgrades. |
What the client said:
This site had difficulties which we as a team had to overcome. Buy-in from the supply chain was crucial to the success of the project as this was the first time Machine Control technology was used in the country. The support and encouragement from Transport Scotland allowed us the opportunity to innovate. Collaborating with R3 and Topcon to shift away from traditional methods was a pleasure. The results, including an F1 racetrack-standard milled surface, showcase the project’s success. The improvement in IRI is clearly demonstrated in the data produced by the digital model.
Want to see what’s possible on your next project?
R3 Ltd specialises in bringing racetrack-grade precision and next-generation surfacing solutions to real-world roads — delivering smoother finishes, lower costs, and longer-lasting results.
Whether you’re tackling complex resurfacing challenges or looking to futureproof your assets, our team is ready to help.
Get in touch to find out how R3 Ltd can support your next project.